1. Introduction to Tin Ore
Tin ore, one of humanity’s earliest utilized metals, played a pivotal role in ancient bronze production. Today, its ductility, corrosion resistance, and non-toxic properties make it indispensable in modern industries, electronics, and renewable energy technologies. Tin primarily exists in two forms: alluvial/sand deposits and hard rock veins, each requiring tailored processing methods.
2. Key Tin Ore Processing Methods
2.1 Gravity Separation
The cornerstone of tin ore processing, gravity separation exploits the density difference between tin (6.4–7.1 g/cm³) and gangue minerals (2.5–3.0 g/cm³). Widely used for both sand and rock tin ores, it ensures cost-effectiveness and environmental sustainability.
3. Processing Alluvial/Sand Tin Ore
3.1 Workflow Overview
Feeding
- Equipment: Vibratory feeders, hoppers, or excavators.
- Purpose: Remove oversized debris via grizzly bars.
Washing
- Equipment: Trommel scrubbers (for clay-rich ore) or trommel screens.
- Purpose: Eliminate clay and mud to improve separation efficiency.
Screening
- Equipment: High-frequency vibrating screens.
- Purpose: Classify ore into sizes for optimal jigging.
Primary Concentration
- Equipment: Jig separators (e.g., diaphragm jigs).
- Outcome: 60–70% tin concentrate.
Final Concentration
- Equipment: Shaking tables.
- Outcome: 90%+ high-grade tin concentrate.
Refining (Optional)
- Equipment: Magnetic separators.
- Purpose: Remove iron, ilmenite, and other impurities.
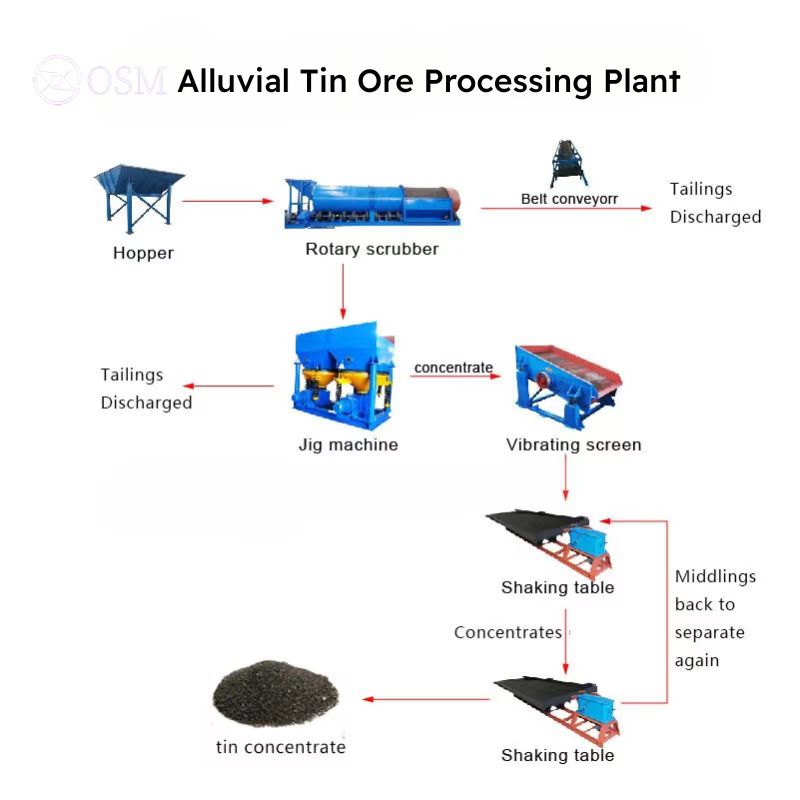
4. Processing Hard Rock Tin Ore
4.1 Workflow Overview
Crushing
- Equipment: Jaw crushers → Cone crushers → Hammer crushers.
- Target: Reduce ore to 10–20 mm particles.
Grinding
- Equipment: Ball mills or wet pan mills.
- Purpose: Liberate tin particles from quartz or granite matrices.
Gravity Separation
- Repeat steps 3–6 from alluvial processing.
- Additional: Rod mills may refine particle size pre-jigging.
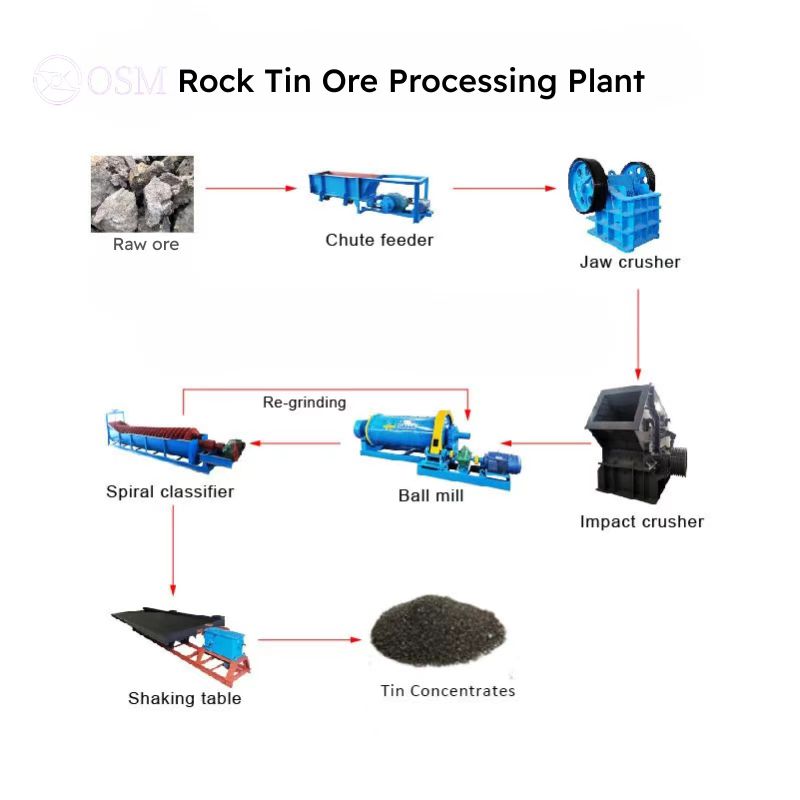
5. Critical Equipment in Tin Processing
Equipment | Function | Applicability |
Jig Separator | Primary concentration via pulsating water | Alluvial & Rock Tin |
Shaking Table | Final refinement of tin concentrate | Alluvial & Rock Tin |
Magnetic Separator | Remove magnetic impurities | Post-concentration stage |
Trommel Scrubber | Clay removal & pre-screening | Clay-rich Alluvial Ore |
6. Industry Leader: OSM Mining Equipment Co., Ltd.
With 20+ years of expertise, OSM provides end-to-end solutions for tin ore processing, from customized flowcharts to on-site commissioning. Their plants operate globally, including in China, Nigeria, and Mongolia, achieving recovery rates of 85–92%.
7. Conclusion
Successful tin ore processing hinges on ore type identification, proper equipment selection, and optimized gravity separation. Whether dealing with alluvial deposits or hard rock veins, a systematic approach ensures high recovery and profitability.
Need a customized tin processing solution? Contact experts for a tailored plan!(joey@oreequipment.com)
Note: Flowcharts and equipment images are simplified for illustration. Actual plant design requires ore testing and engineering analysis.